GWC2-1250/2150型钢网多头点焊机
使用说明书

一、概述:
GWC2系列钢网多点点焊机是生产电焊网网片的专用自动焊接设备。它可以用于焊接建筑行业轻体墙板的舒乐舍板网,高速公路及铁路护栏网的制造、商场及大型超市展品用网片及其它用途的各种护栏网的生产制造,能够焊接直径2mm-6mm的低碳钢、低合金钢及其镀锌丝的焊接,配上先进的焊接控制器及专用焊接电极,也可以用于不锈钢和黄铜等材质的高质量焊接。产品具有设计合理、造型美观大方、自动化程度高、焊接性能稳定可靠等特点,由于本机采用板框式机架结构和大功率焊接变压器及专用焊接控制装置,所以能够高质量地完成不同丝径,不同目数的各种焊网的焊接要求,与同类产品相比焊接范围更大、焊接质量更高、节约电能更多、工作稳定性更高。
产品说明:
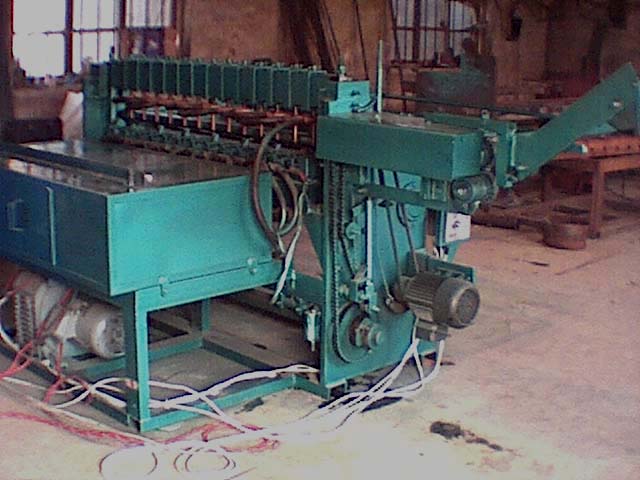
焊机左侧外观
焊机左后侧外观
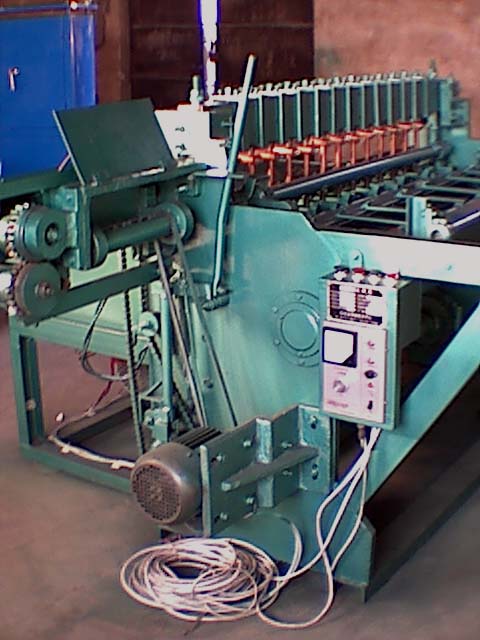
经丝调直装置
纬丝调直装置
二、主要技术参数:
1、焊幅宽度(mm)1250、1550、1850、2150
2、网目规格(mm)25.4-203.2(1”-8”)
3、焊网丝径(mm)φ2.0-φ6.0(BWG5-BWG14)
4、焊网速度(目/分钟)15-50(径向)
5、电源类型:三相380V±10% 50HZ
6、焊网变压器容量:150KVA-315KVA
7、加压方式:气动或电动凸轮方式
8、电机调速方式:电磁调速或变频调速
9、纬丝送丝方式:自动调直送丝或料斗摆动送丝
10、经丝送丝方式:电动偏心轮或步进电机
三、安装与调试:
1、焊机及控制柜的安装:
因焊机主机结构均为机械传动结构,工作时产生的振动较大,为确保焊接工件的产品质量,建议主机设备能打地脚螺丝固定安装,并尽量保证工作焊接面的水平。控制柜建议放置在焊接设备主机的左侧,距主焊接设备的距离应大于2.5米,以减少焊接设备对控制柜的干扰和影响,同时也方便操作人员的调整和调试。为保证操作者的安全和减少周围其它设备对本焊机的干扰,控制柜和焊接主机都应安装接地线,接地线的接地电阻≤4欧姆。
2、经丝料盘的固定架安装固定:
因焊机本身不带经丝料盘及固定架装置,用户应根据经丝盘的尺寸大小自行设计经丝及料盘架装置,为保证经丝在焊接过程中的张力,经丝盘固定架的出丝高度应不低于1.2米,固定架的出丝口距焊接主机之间的距离应不小于5米,用户可参考附图自行设计经丝放丝盘及固定架的尺寸。
3、纬丝料盘及固定架的安装:
因焊机本身不带纬丝料盘及固定架装置,用户应根据实际情况自行设计该部分的结构及尺寸,为防止纬丝在工作过程中松脱及缠死,纬丝应有防松脱及卡死装置,因纬丝送料速度远远大于经丝送料速度,因此必须解决好纬丝的送料工艺工装,必要时应安装防滑带阻尼的纬丝盘送料的装置,纬丝盘上的纬丝尽量不要乱绕工艺,如有条件的话应采取精绕工艺。纬丝料盘固定架应与焊机主机纬丝送料轴平行,两者之间间距应大于3米。工作时为防止纬丝折断或拉到末尾端甩出伤人,操作者应随时注意工作时的纬丝送丝情况,出现异常应立即停车处理,有条件的用户可用弹簧护套或穿管的方式把距离操作人员较近的部分保护起来。
4、用户的电源要求及接地要求与安装:
因本焊接设备的焊接功率较大,对电源的供电也有较高的要求,用户供电变压器的容量应不小于160KVA,供电变压器到焊机主机的实际用线距离应小于200m,如用户不能达到以上条件时必须加大供电变压器的容量或增大输电线的截面积,否则可能影响焊接效果。主电源线应使用不小于 50mm2 的铜质导线,设备应单独使用一块不小于250A的石板闸刀开关或400A的空气自动开关,保险的容量应大于250A。
焊机的主机与控制柜机壳都应安装接地线,接地线的接地电阻≤4欧姆,接地线应使用不小于4mm2的铜质导线进行安装,为确保设备的正常运行和操作者的人身安全,安装合格的接地线也是非常重要的一项工作。
因焊机采用三相四线制,在电源引线时也应把零线接至主开关附近,并且单独使用一块刀闸进行控制,需注意的是零线开关上是不能安装保险丝的,否则机器将不能正常工作。零线应使用不小于4mm2铜质导线进行连接。
5、电源与控制柜、控制柜与主机之间的连线:
控制柜的进线侧在控制柜右侧下端,共有A、B、C、D四个接线端子,其中A、B、C线为相线,应使用不小于25mm2的铜质铜线与电源开关接在一起,D为零线,使用4mm2的铜质导线连接在零线开关上,需注意的是:零线与焊机设备的接地,线是不同功能的两条独立线,两者绝对不能混淆。
焊机控制柜与焊机主机焊接变压器之间的连线用不小于25mm2的铜质导线进行连接,连线尽可能的短并尽量接触良好,焊机主焊接变压器接在焊机后侧正中间位置,控制柜焊接输出位置在控制柜右侧下侧。A、B为一台或一组变压器连线,B、C为另一台或一组变压器连线,个别宽幅产品型号会有第三组输出连线A、C,只要连接在第三台或第三组变压器上即可。
焊机主机主电动机的三相电源线接在控制柜左侧下侧偏左位置的电机输出端上,该电机的励磁部分其中一根线接在该三相的任何一相上,另外一根线接在零线上即可。主电机的激磁绕组和测速发电机输出端共5根线与调速表连线请参考附图进行接线。焊机的纬丝调直电机(辅助电机)接线接在控制柜左下侧右侧的辅助电机输出端上。
焊机主机控制按钮至控制柜之间连线为2条3芯连线,红色为常开,蓝色为公用,绿色为常闭,该两条线通过控制柜左侧穿线孔引入控制柜接在相应的接线端子上。焊机主机焊接控制接近开关的连线为两芯屏蔽线,连接在控制柜内部控制线路板上。需注意的是:控制器两芯线红色(或黄色)为电源+12V,绿色(蓝色)为控制输出,屏蔽层为12V地。
四、调试与运行:
焊接设备的调试分机械部分调试和电控部分调试两部分,一般情况下应先对机械部分进行调试,由于设备出厂时已经提前按用户要求的焊接工件类型进行过调试,当焊接工件未发生变化时一般不需较大的调整,机械部分的调试步骤如下:(1)在调试前应将焊接控制接近开关的控制开关搬至调试位置,此时在焊机焊臂压下时焊接控制器及焊接主变压器均不工作;(2)将欲焊接的经丝经过调直装置或缓冲装置穿过定位导板孔后穿过焊接电极放置在工作平台上;(3)将纬丝盘中的纬丝通过纬丝调直机构穿至焊机主机定位切断处;(4)同时开启主电机和辅助调直电机检查电机运转方向是否正确,检查纬丝的自动切断长度是否够长,是否送到位,如有问题需对纬丝的送丝装置进行调节;(5)连续几次观察送丝情况如无问题则可进行焊接,并观察焊接后的经丝沿经向移动情况,同时测量经向移动距离是否在允许范围内,如超过偏差就须对经丝送料机构进行调节;(6)检查焊接工件的成形及焊后强度,如无问题则可进行批量焊接,在定长度焊接时应把控制柜内计数器开关打开,并对计数器清零和设置数值,如定长4米的10CM网孔只要设为0040即可,当焊接够长度后主电机和辅助电机同时自动停止工作;(7)工件从定长处用自动剪板机切断后的网片进行码装,完成整个焊接过程。
电控部分的调试:电控部分调试由焊接变压器的接触组插把调节,控制器焊接时间及焊接能量的调节,焊机主机控制接近开关位置的调整,焊接电极压力调整等。具体调试调节方法如下:
(1)焊接主机焊接变压器容量在40KVA以上时,一般都随变压器安装相应的接触组插把装置,用于调节变压器的输出电压,插把共有三套,每个插把有两个位置,共八种电压,具体电压值请参考附表说明。调档的位置应根据焊接工件的粗细进行适当选择。当焊接φ2.0mm的钢丝时,可选择较低的档位,当焊接φ5.0mm的钢丝时,则应选择较高的档位。
(2)焊接控制柜中控制器焊接能量及焊接时间的设定和调试,此部分可参考随机配带控制器相应型号的焊接控制器说明书进行调节,对于网片类焊接工件,一般希望采用大规范焊接,这样工件焊后变形小,外型美观。在没把握的前提下应先选择较低的焊接电压和较短焊接时间,经试焊后如焊接强度不足再逐渐加大焊接电压和延长焊接时间,直到达到工件的焊接强度和外观要求。
(3)焊机主机上控制用接近开关的位置调节,主要是实现在焊接过程中控制给火焊接的时间早晚,一般掌握的原则是上电极压紧工件后开始焊接,当上电极下压至最低位置时焊接结束,这样才能保证工件的焊接性能。当给火时间过早,可能因压力过小把纬丝烧坏,当给火时间过晚,网片的焊接强度较低且外观不好。
(4)焊接电极压力的调整是为了保证焊接压力的调节和上电极伸出长度的调节而设定的。为了保证要焊接的几根至几十根经丝的压力都一致,必须对每一个上电极的压力大小进行适当的调整。当焊接压力调整过大或过小时,都会影响工件的焊接性能,尤其是在串联电极焊接方式中更为重要,当调整不合适时根本就不能焊接,形不成焊点。
因焊机主机设备采用凸轮、偏心轮装置实现焊接需要的全机械控制过程,因此焊机设备的润滑也就成了设备运行过程中不可缺少的一部分工作。用户在使用设备时应经常对有机械摩擦、机械传动的部分进行润滑,在主机中设了一些注油孔或油杯,应及时对设备进行润滑,一般情况下每班加注润滑油的次数不应少于三次,以减少设备的正常磨损,延长设备及其配件的使用寿命。
五、常见故障现象及处理:
故障现象1、焊接设备空载调试正常,只要一焊接就停止工作。
故障产生原因及排除:出现此类故障现象,一般都是因为电源供电不足所致,空载调试时电网电压基本正常,当正常焊接时因耗电电流迅速加大导致电压过低,从而不能保证交流接触器等组件的正常工作。处理方法是从根本上解决电源供电问题,在焊接过程中电压最低极限不能低于340V。
故障现象2、电源三相电正常,启动电路风扇和调速电机均不工作。
故障产生原因及排除:上述故障的原因是在三相电源供电正常的前提下,如果供电的零线没有接好或接触不良,那么会使得冷却风扇、调速电机的电磁调速器不能正常工作,只要把零线接好即可解决问题。
故障现象3、焊接设备空载调试正常,焊接时无焊接输出,工件不焊接。
故障产生原因及排除:出现上述故障,一般由以下几种情况,请参照电原理图进行检修。(1)接近开关调整不合适,距离定片检测片太远;(2)接近开关供电的12V稳压电源有问题或线路接触不良;(3)接近开关碰坏或内部有质量问题;(4)焊接/调试开关没有打在焊接位置;(5)电磁继电器J3触点接触不良;(6)焊接控制器电源开关未打开;(7)焊接控制器输入、输出线接触不良。
故障现象4、焊接工件的焊点强度大小不均匀或有个别焊点不焊接。
故障产生原因及排除:产生此类问题的关键是上下电极高低不齐或接触平面不平整及电极压力不均匀所造成的。一般情况下是因为上下电极的接触面使用时间长,导致平面不平整(有凹槽)或粘有氧化皮等杂物对工件的焊接造成影响的,只要修磨电极即可解决。
故障现象5、焊接设备的电磁调速电机速度调整不灵敏或不能调整。
故障产生原因及排除:出现上述故障,一般是调速电机电磁调速器(型号JD1A)内部元器件有质量问题或接触不良,一般在排除外部接线错误及接触不良的原因后,应参考随机附带的交流电磁调速器使用说明书进行调整和检查。
故障现象6、焊接工件的焊点强度太小或过大。
故障产生的原因及排除:出现上述情况,一般是由于焊接时间,焊接能量的调整不合适所致,用户应参考随机附带的KD2-160A或KD5-250A焊接控制器的使用说明书,对焊接能量和焊接时间进行调整,具体焊接参数应根据焊接工件的焊接性能进行调整,掌握的原则是大电流短时间则焊接效果较好,反之则效果较差。需特别注意的是个别焊点的差异,最好检查相应上下电极方面的问题,不要随意地调节焊接时间和焊接能量。
故障现象7、定长焊接时焊够焊点数机器不自停。
故障产生原因及排除:出现上述问题原因是定长焊接开关未打开,焊接计数器JDM9-4未正常工作,一般只要计数器能正常计数,只要打开定长控制开关即可。如果计数器不能正常计数,则应检查其外围接线是否有接触不良或者计数器本身产生质量问题,需对计数器进行修理或调换。
故障现象8、按下主机设备的启动钮,主电机和纬丝调直电机不工作。
故障产生原因及排除:出现上述故障的原因是36V交流电源供电有问题或控制按钮接触不良,也有可能是因电源线缺相导致电动机过热使热继电器动作,最常见的故障问题是定长尺寸焊接到长度时计数器控制切断主电机控制回路,只要按一下计数器的复位按钮即可正常工作。
故障现象9、焊接过程中纬丝偶尔出现送料长度不足。
故障产生原因及排除:出现上述情况是由于纬丝盘中的纬丝缠绕不均匀,在送丝过程中出现纬丝拉不动造成送丝轮滑动而使得送料长度不足。应重点把纬丝盘中的焊料缠均匀后再进行焊接。有时送丝轮之间的压力调整较小也可能产生上述情况。
故障现象10、焊接工件的网孔径向成型不好。
故障产生原因及排除:出现上述问题的原因是经丝张力不够或张力不匀,个别经丝张力过大或过小。应重点检查经丝盘的送料情况,尽可能把所有经丝的张力调整的尽可能差不多就行了。
六、随机配件及保修说明:
为保证设备出厂后能够正常工作,生产厂家已将常用易损备件随机配备,用户也可根据需要另行定做加工购买易损配件,随机配件清单如下:
(1)焊接上电极 5-20套(最少按焊点的20%配备)
(2)焊接下电极 5-20套(最少按焊点的20%配备)
(3)按钮开关 4只
(4)接近开关 1套
(5)钮子开关 4只
(6)保险管5×20 0.5A 4只
(7)RL-15瓷保险芯 6只
根据国家有关规定,焊机自出厂之日起保修一年,属于产品制造原因造成的技术故障由生产厂免费维修,属于用户原因造成的故障由用户负担维修费用,当责任原因不明时双方各承担50%的维修费用,但是对于有机械磨损的易损元件不在保修范围内:
1.控制按钮
2.控制开关
3.控制器面板元件
4.交流接触器 5.交流电动机
6.焊接电极
7.机械传动零件 8.保险芯管
9.焊接电缆及接头
10.连接螺丝
焊接设备在使用过程中有任何问题请及时与我公司联系协商处理,我公司会提供强有力的技术支持。
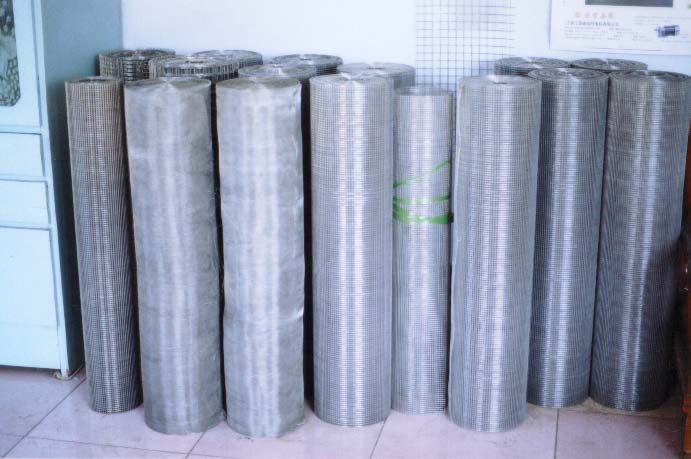
返回
|